In demanding mining environments, the design and maintenance of load zones and transfer points are crucial for ensuring smooth, safe, and efficient material handling.
By Jonathan Rowland
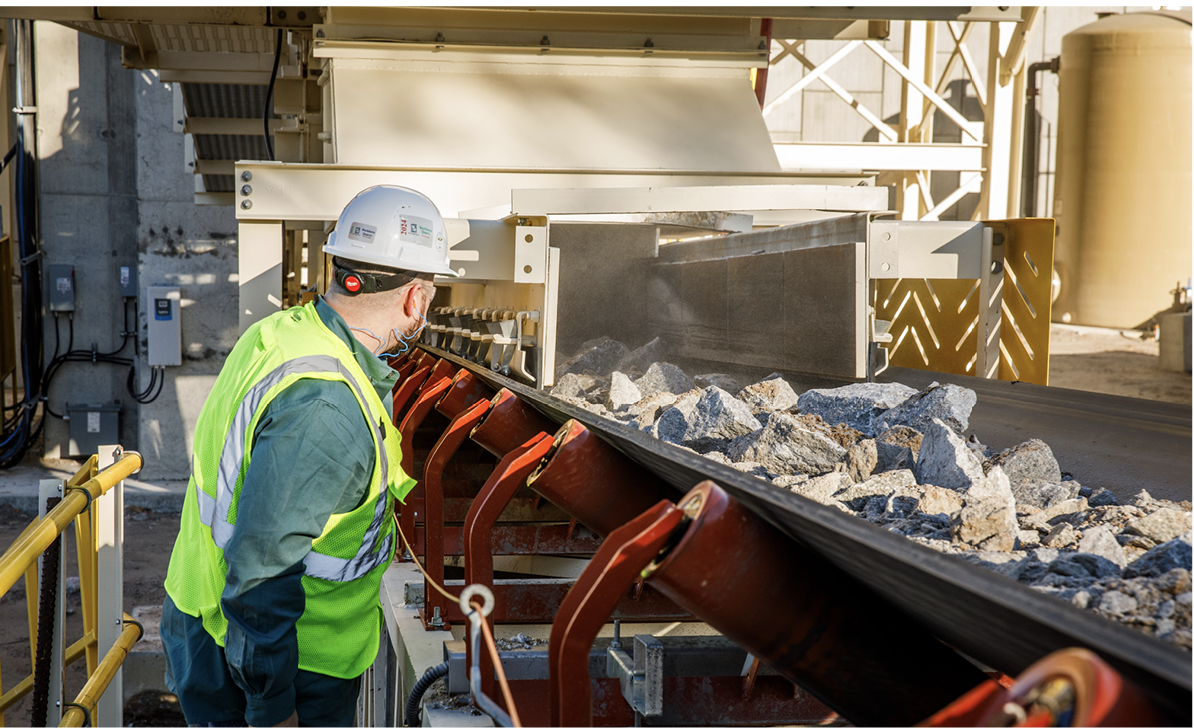
Load zones and transfer points are critical areas in any belt conveyor system. Properly designed, they help stabilize the belt and prevent bottlenecks, ensuring smooth and continuous material movement. They also help minimize spillage and dust, enhancing operational safety and creating a healthier working environment.
When well-maintained, transfer points help prevent conveyor belt wear, reducing maintenance costs and downtime. Investing in the correct design and upkeep of these vital areas is, thus, fundamental to achieving long-term operational success in bulk material handling.
According to the experts who spoke to North American Mining on this topic, key considerations in load zone and transfer point design include:
- Material characteristics (e.g., abrasiveness and lump size).
- Minimum chute slope angles.
- Adequate area in the transfer chute and receiving
loading area. - Slope angler of the receiving conveyor.
- Available height for transfer.
- Material trajectory control.
- Ease of inspection and maintenance.
“Incorporating flexibility in the design ensures adaptability to varying operational conditions and material loads,” added Riley Arndt, strategic account manager for Superior’s Conveyor Components division.
In addition, “without the suitable components installed at the loading zone, dust and spillage is inevitable,” Jerad Heitzler, training manager at Martin Engineering, told North American Mining. “Proper skirting systems along the chute are critical to sealing the load zone. The belt must also be stabilized with support cradles or closely spaced idlers to eliminate belt sag between the idlers, which can cause gaps for dust and fugitive material to escape. By ensuring the belt remains flat and stable, the skirting system has the proper surface to seal against.”
Design tools, such as computational fluid dynamics (CFD) analysis and discrete element modeling (DEM), are essential in designing appropriate transfer zones, allowing “designers to analyze flow and chute wear for all loading conditions using the correct material characteristics,” said Todd Kirkpatrick, director of engineering at Continental Conveyor, a division of PPI.
CFD is “instrumental in understanding how material and airflows behave during transfer,” agreed Arndt. “By simulating conditions like turbulence or dust dispersion, designers can pinpoint inefficiencies, such as material scattering or bottlenecks, and make adjustments to improve flow. CFD also helps optimize designs for dust control by predicting where particles are likely to escape and addressing those areas pre-emptively.”
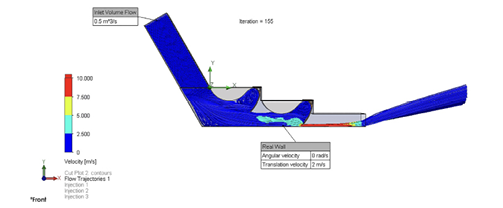
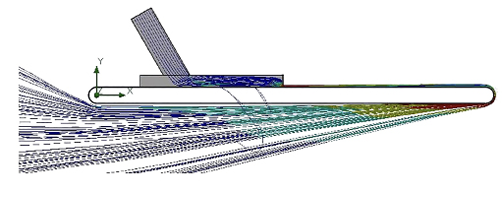
Graphic: Martin Engineering
Controlling dust
Dust is one of the significant issues in transfer point design, impacting air quality and worker safety. Dust is “primarily generated when materials free-fall onto conveyor belts, creating turbulence,” continued Arndt. “Effective dust control begins with reducing material drop heights and using stilling zones to allow dust to settle. Dust suppression systems, such as barriers or water misting, can contain fine particles, while regular cleaning and maintenance ensure systems remain effective over time.”
Picking up the dust issue, Heitzler highlighted the CFD airflow model in Figure 1. “As this model shows, dust emissions are inevitable without strategically placed dust curtains, regardless of chute design, as the impact of tons of heavy raw materials created incredible turbulence within the chute. Strategically installing dust curtains based on such modeling slows air velocities, allowing dust to settle in the materials stream. On shorter loading enclosures, dust bags at the end of the settling and stilling zones give excess air a place to escape, as the fine mesh collects the particulates. During shutdowns, the collected dust is deposited back onto the conveyor.”
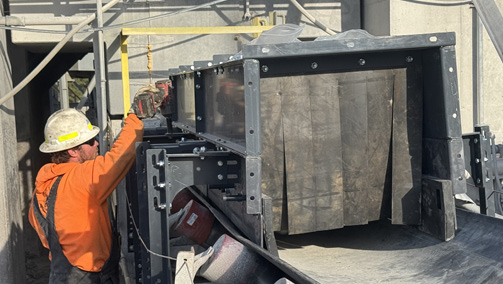
Load zones and transfer chutes in mining applications
The “harsh conditions found in mining applications – abrasive materials, heavy loads, and fluctuating temperatures – exacerbate wear on load zone components,” explained Superior’s Arndt. “High impact forces can lead to belt and structural damage while dust and fine particles can infiltrate moving parts, causing operational inefficiencies and requiring frequent cleaning. Designs must focus on durability and resilience to address these issues, such as abrasion-resistant materials and shock-absorbing supports.”
“Protecting receiving equipment is essential in mining applications,” agreed Kirkpatrick’s colleague and principal engineer at Continental Conveyor, Larry Atkinson. “However, this protection should be balanced with providing efficient material flow during all loading and environmental conditions.”
Martin Engineering’s Heitzler pointed to the issue of carryback as an example of a specific challenge conveyors in mining applications face. “Vibrations caused by the loaded belt cause dust and fine particles that are not shed as emissions to settle on the belt surface under larger and heavier cargoes. This places this fine material under pressure. As a result, it adheres to the belt surface and lodges in cracks and divots so that, at the discharge zone, it remains on the belt and enters the belt return rather than the discharge stream, becoming carryback that is shed as dust emissions or spillage that piles under the system (Figure 2).”
This carryback can impact air quality and equipment life as fine particles penetrate machine parts and rolling components, continued Heitzler. Spillage can also “cover walkways, restrict access to the system, and require labor for cleaning. This raises operating costs.”
Underground mines present additional challenges, notably limited space and stricter ventilation requirements. “Dust control is, thus, a more critical concern,” said Arndt, “while maintenance is complicated by limited access to equipment, often requiring creative design adjustments to facilitate easier inspections and part replacements. Additionally, operators must account for the added strain of working within these constraints, emphasizing ergonomic and efficient designs.”
“Combustible dust is an additional major concern in underground environments,” added Heitzler. “A belt fire can spread fire at lightning speed from one conveyor to the next and burn for hours, causing an emergency across the entire mine faster than many can react. This can ignite methane deposits and reduce air quality throughout the operation. This is why comprehensive dust control using the latest designs and components installed and monitored by knowledgeable service professionals is essential.”
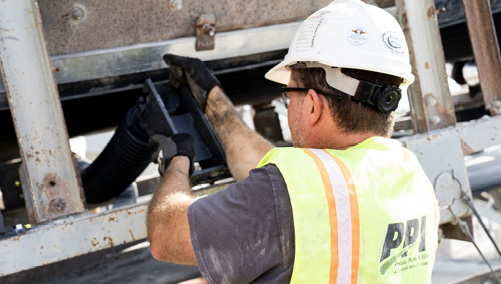
Conveyor safety
Continental Conveyor’s Kirkpatrick noted that limiting machine-human interactions through good design is the first step to safe load zone operations: “prevent plugging, spillage, and minimize dust to limit maintenance, containing material in the transfer chute and load zone.”
“Load zones are often in confined spaces with heavy, fast-moving materials posing a risk to operators,” added Superior’s Arndt. “Designed should prioritize guarding, easy-to-access maintenance areas, and ergonomic adjustments to reduce manual strain. Clear signage and regular safety audits are essential to mitigate risks during inspections and adjustments.”
Martin Engineering’s Heitzler also noted ease of maintenance access as critical to conveyor safety. For example, external wear liners eliminate the need for confined space entry and hot work traditionally associated with wear liner replacement.
An external skirting system may allow adjustment and replacement from outside the conveyor system. Many impact cradles and belt support systems can also be designed for inside-the-transfer-point slide-in/slide-out installation and replacement.
“Being able to perform as much maintenance and parts replacement from outside the system rather than crawling underneath or breaking the belt plane is the key to safe conveyor servicing,”
Heitzler concluded.
Training and education also play a role in safety.” Mines should ensure operators and maintenance technicians are educated on the correct function of each transfer point component,” said Continental Conveyor’s Atkinson.
Maintenance and retrofits
Maintenance intervals “depend on the operating environment and material characteristics,” said Superior’s Arndt, “but should be frequent enough to catch wear before it escalates. Weekly checks might focus on visible spillage, dust accumulation, and belt alignment, while monthly inspections can address wear on structural components, fasteners, and sealing systems. A systematic schedule ensures consistent performance and reduces unplanned downtime.”
“Maintenance should be performed on schedule with general conveyor inspection, realizing that the transfer point is the most critical maintenance location,” added Continental Conveyor’s Atkinson. “The key components to inspect are receiving conveyor impact beds and idlers, conveyor belting, wear liners, belt cleaners, discharge pulley lagging, and skirt boards.”
Martin’s Heitzler also highlighted the importance of regular inspections, noting key indicators of issues include “excessive dust emissions, spillage, belt mistracking, extreme belt temperatures, seized idlers, and slippage from fouled pulleys.”
When considering a load zone/transfer point retrofit, the challenge “lies in enhancing performance without extensive downtime or re-engineering,” said Atkinson.
“It is crucial to assess the existing system for weak points – excessive wear, misalignment, or spillage – and target those with modular, flexible solutions. Simple upgrades like better sealing mechanisms or adjustable skirting can make a significant difference.”
Heitzler added the following considerations as his retrofitting best practices:
- Control the material flow with a sloped or scoop-shaped transfer chute, allowing for less impact on the belt and centered loading.
- Ensure the belt is centered when entering the loading and discharge zones and along the cargo and return paths. Modern tracking systems can achieve this.
- Reduce the distance between idlers or install cradles to eliminate belt sag.
- Install external wear liners and skirting to protect the chute wall from erosion and create a sealed environment in the transfer zone.
- Hire a professional to supervise and/or perform
the design and installation for the best results.
Ensuring the best flow
Load zones and transfer points are essential to efficient mining operations. By optimizing these areas through good design and maintenance, alongside considered retrofits, mines can achieve smoother, more reliable material flow, increase productivity, and reduce operational costs.